Advancing Medical Device Prototyping with Die-Cutting
Written by Jeff Davis
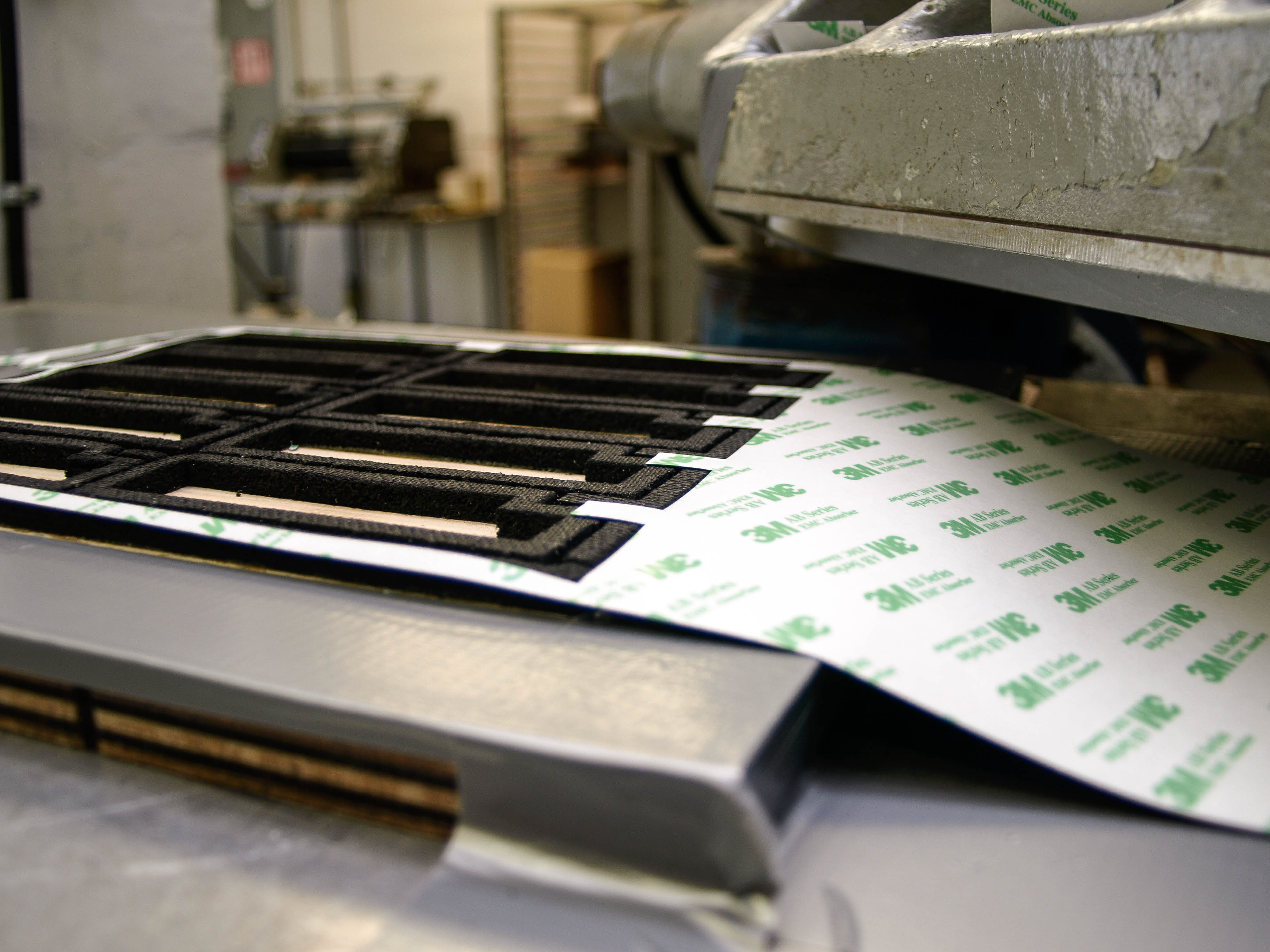
Rapid prototyping of medical devices is crucial in the development process, enabling designers and engineers to test and refine products before full-scale production begins. However, traditional medical device product development can be time-consuming and costly — slowing time-to-market.
Medical device prototyping using die-cutting offers an efficient way to streamline the process and accelerate the entire production cycle. Because digital die-cutting does not require custom tooling, the process is fast and significantly less expensive.
How Die-Cutting Services for Medical Devices Accelerates Manufacturing
Die-cutting is a subtractive manufacturing process that involves the use of blades and rules to cut intricate shapes and patterns from various materials. This makes it a versatile solution for prototyping.
Medical device prototyping can effectively utilize die-cutting for a wide range of applications, such as:
- Wearable medical devices
- Wound care essentials
- Surgical attire
- Advanced drug delivery systems
- Medical tubes and catheters
- Diagnostic strips
- Orthopedic supports
Medical device prototyping with die-cutting creates a highly precise and accurate model for testing, even for intricate designs and complex adhesive patterns. This allows designers and engineers to explore innovative concepts at low costs while accelerating the product development cycle.
The Benefits of Rapid Prototyping
By leveraging custom die-cutting for medical devices, manufacturers can produce rapid prototypes. Before full-scale production starts, engineers can:
- Refine product design: Identify any potential flaws or issues to make improvements to the final design parameters.
- Test real-world materials: See how materials perform, look, and interact in the real world vs. computer simulations.
- Test environmental conditions: Confirm that materials and design will withstand harsh conditions or other environmental factors.
- Test manufacturing processes: Fine-tune the manufacturing process to create higher-quality products and avoid costly errors.
- Improve safety and compliance: Meet company, industry, and regulatory compliance.
- Reduce costs: By identifying modification needs across design, materials, or production, you can save money on final product production and reduce risks.
When you are developing an innovative medical device or new designs, you may need to modify materials to exacting specifications. A prototype that you can see, hold, touch, and test helps visualize the end product, giving stakeholders a more tangible way to evaluate products, and helping to streamline decision-making.
Few manufacturers understand the complexity and regulations of the medical industry, so you need to work with a trusted custom materials converting partner that has deep experience.
How Tapecon’s Die-Cutting Services Streamline Product Development
By integrating die-cutting with other manufacturing processes, such as laminating, slitting, and converting, Tapecon offers a comprehensive suite of solutions that streamline the prototyping and production phases. Tapecon’s experts can turn designs into tangible prototypes by working closely with engineering teams.
As a 3M Preferred Converter and Consumables Value-Added Reseller (VAR), Tapecon offers more than just products—they deliver tailored, innovative solutions to meet the specific needs of the medical device industry.
Your Invitation to Innovate
The medical device industry is constantly evolving, and it's crucial to have a partner who can keep up with the pace. At Tapecon, we understand the complexities of this industry and have the right technology and expertise to help you stay ahead of the game. Our die-cutting services are a testament to our commitment to advancing healthcare technology and can help transform your medical device concepts into market-ready realities.
Contact us today to learn more about our die-cutting prototyping services and accelerate your path to innovation and success.
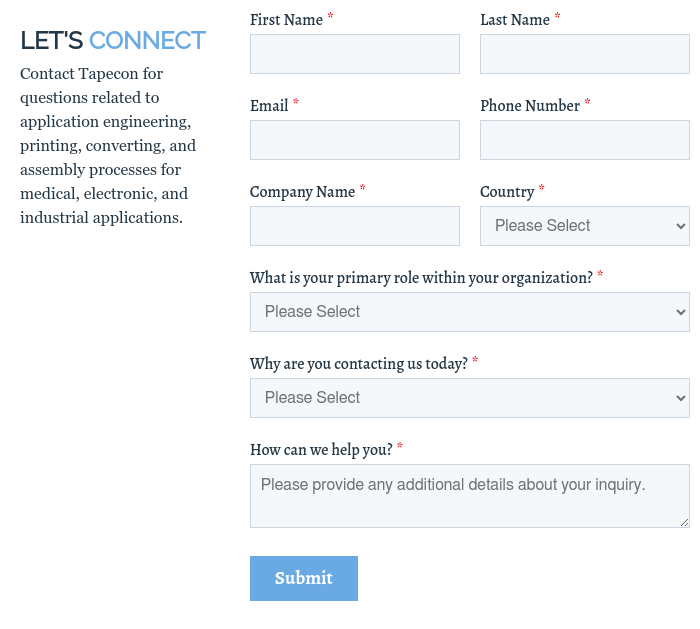