From Lab to Scale – Designing with Manufacturing in Mind
Written by Rafael Tudela
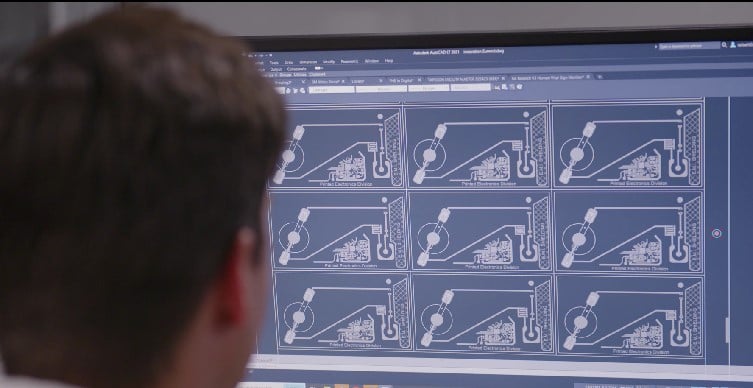
Many of today’s most innovative products are being designed and prototyped in cutting-edge labs and research centers. These environments foster creativity and allow for the development of groundbreaking technologies. Unfortunately, product teams often find that their carefully designed product cannot be manufactured at scale, sending them back to the drawing board and delaying the product's journey to the market.
In this article, we will cover why, when, and how to get a manufacturing partner involved in the design process to bridge this gap and ensure successful production at scale.
But first, let’s talk about s’mores. What does this have to do with manufacturing? More than you think.
A tasty analogy
Imagine you’re tasked with making a s'more. The ingredients for this classic treat are typically two graham crackers, a marshmallow, and a piece of chocolate. The processing steps are straightforward – toast the marshmallow, then break the graham Cracker and chocolate. Finally, the assembly is simple – put chocolate on the graham cracker, put the toasted marshmallow on the chocolate, then finally sandwich with another graham cracker. Eat and enjoy!
Now, consider the scenario where I ask to make 1,000 smores. Suddenly, several questions arise. How fast can you make them? Can you guarantee repeatable results? Can you customize it to my preferences? Can you meet my price point? And what if the demand increases to 10k, 50k, or more?
The likelihood is that your design and process would need to change. This change is illustrated by the MacLeamy Curve, which shows that as a project progresses through the design process, the cost of design changes increases significantly. The takeaway is that it is extremely beneficial to introduce a manufacturing partner at the design development stage – after the preliminary design but before the construction documents are finalized.
Benefits of working with a manufacturing partner
Based on your product and internal capabilities, you can consider bringing in a manufacturing partner for several roles that align with levels of the technology readiness level (TRL) or manufacturing readiness level (MRL) scales.
- Advisory role – During TRL3: Experimental proof of concept
- Consultant role – During MRL 3: Manufacturing proof of concept
- Manufacturing role – During MRL 4: Produce technology in lab
Getting a manufacturing partner involved early in the design process is crucial for several reasons:
- Bridging the “Innovation Valley of Death” – This is the phase between research and successful innovation. Often, promising research does not translate into marketable products – a gap called the 'valley of death.' A manufacturing partner can help bridge that gap and help bring your idea to market.
- Design feasibility for manufacturing – A manufacturing partner can provide insights into the design's manufacturability, including material selection and process recommendations.
- Reliable supply chain – A manufacturing partner can streamline and solidify your chain, ensuring that the necessary materials and components are readily available and at the best price.
- Quality systems – Experienced manufacturers have quality systems in place to ensure that the final product meets the required standards and specifications.
- Compliance with industry standards – Qualified manufacturing partners should be knowledgeable on industry standards such as ISO, ITAR, and UL. And they can ensure that the design and production process complies with these standards.
Design for manufacturing considerations
When it comes to designing for manufacturing, there are several key considerations to keep in mind.
- Understand the trade-offs between the state-of-the-art (the highest level of general development) and the state-of-the-practice (the current standard of applied development).
- Determine specific material requirements rather than specifying particular materials, allowing for greater flexibility and cost-effectiveness in the manufacturing process.
- Tight tolerances should only be applied when necessary, as they can significantly increase manufacturing costs.
- Do not underestimate the costs of manufacturing.
- Be aware of the necessary approvals in your industry.
To find a suitable manufacturing partner, start by defining your scope and manufacturing needs. This will help you narrow down potential manufacturers who specialize in your industry and can meet your requirements. Next, research manufacturers within your industry, looking at their experience, capabilities, quality systems, and compliance with industry standards. Finally, negotiate terms and agreements with the manufacturer to establish a mutually beneficial partnership.
What does scaled manufacturing look like?
Let’s go back to the s’mores analogy. Compared to a one-off product, here’s a hypothetical example of producing a delicious treat at scale.
- Ingredients: Two Fudge Strips™ cookies, one marshmallow
- Processing: Toast the marshmallow in the MallowToaster 3000
- Assembly: Sandwich the toasted marshmallow in between the cookies
As you can see, in scaled manufacturing, the process is streamlined and optimized for efficiency, repeatability, and cost-effectiveness. Materials (aka ingredients) may be substituted for equivalents that are more readily available or cost-effective, specialized equipment may be used to speed up processing, and the assembly process may be automated or semi-automated.
At Tapecon, we have experience working with product teams at all stages of development and manufacturing. Our new product introduction support includes materials selection, technical feasibility, prototyping, process validation, and more. Once the design is finalized, we offer a wide range of custom converting and printing capabilities to seamlessly transition to production. All along the way, we offer our insights and capabilities to guide and add value from the concept stage through manufacturing.
Contact us today to start a conversation about how we can support your product development journey.
Let’s make something great
With over 100 years of manufacturing experience, Tapecon works with product teams to solve challenges, create products, and enhance lives. Learn more about our new product introduction support services.