Outsourcing manufacturing is a significant decision for your organization – and one that you don’t want to make hastily. Previously, we discussed the myriad benefits of outsourced manufacturing, including cost savings and freeing your team to focus on its core competencies. For those interested in making the move, we’ve also covered what to look for in a manufacturing partner and why a feasibility study is a critical step in the decision-making process.
Now, let’s talk about what comes after the decision is made. A common question we hear is, “What happens after the contract is signed?” We can’t just flip a switch and instantly transport production from your facility to ours. There are many moving parts (literally) and factors to consider. That’s why a comprehensive implementation plan is imperative to business continuity and the long-term success of the partnership.
While every engagement is unique, here are the four major steps we manage to ensure a smooth transition to outsourced manufacturing.
Step 1 - Prototyping
The first step in the transition process is prototyping. No, we’re not looking to reinvent your product but rather replicate it using our equipment and processes. This can go one of two ways.
- If an existing blueprint is available, we will review the specifications and bill of materials. In some cases, we may offer solutions to optimize the product, such as alternative materials or more efficient converting techniques.
- No blueprint? No problem. Our team will evaluate and reverse-engineer the product. After identifying the layers, we can determine comparable materials and appropriate manufacturing processes.
Step 2 – Project plan and qualification runs
After prototyping, the project plan includes a series of qualification evaluations to validate and verify our manufacturing approach. These include:
- Design qualification (DQ) – Determining what machines will be needed, what processes will change or remain, technical specifications, preliminary testing, purchase order review and more. The final plan must be approved by the director of operations, quality & compliance manager, and a manufacturing engineer.
- Installation qualification (IQ) – Installation and calibration of equipment, along with verification of operating instructions and required safety features.
- Operational qualification (OQ) – Verifying that the process runs as intended, along with establishing operating settings and parameters.
Step #3 – Process qualifications
Once we know how to make the product, we verify that our processes are effective and sustainable under typical operating conditions. This step is called the process qualification, or PQ for short.
Several team members will participate in the PQ, but most important are the operators who will be involved in full-scale production. We verify that the sample production achieves all the critical product specifications. If there is a deviation, it will be noted with a justification of why the qualification is not affected. Proof of the PQ is supported by inspection/test results, data collection sheets, and capability assessment. At the conclusion of the PQ, the run receives a pass or fail result.
Step #4 – Scale for production
Once all the processes are set and the validation and verification are complete, it’s time to ramp up to your desired production volume. This step includes supply chain management to ensure we have ample materials for undisrupted manufacturing.
Even after full production begins, our team always looks for ways to optimize the process. We also hold quarterly reviews to address any issues and make sure both sides are satisfied with the outcomes.
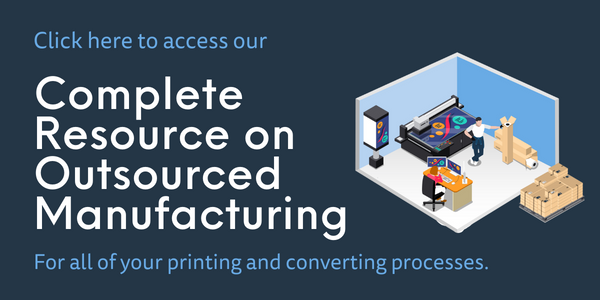
Ready to get started
At Tapecon, we believe that implementation sets the tone for a successful outsourced manufacturing partnership. That’s why we’ve developed and honed a comprehensive transition plan that allows you to realize the benefits of outsourcing as quickly and effectively as possible.
If you have any questions about how your company can outsource non-core manufacturing processes, reach out to our team today.
Let’s make something great
With over 100 years of manufacturing experience, Tapecon works with product teams to solve challenges, create products, and enhance lives. Learn more about our outsourced manufacturing services.