Manufacturing cells combine the benefits of batch and continuous flow manufacturing. While converting a facility to work cells can be a major endeavor, organizations frequently report rapid gains in quality, efficiency, staff performance, and other areas.
When designing a manufacturing cell operation, the main objectives are to create distinct part families within each cell, then organize a cluster of cells to promote an efficient, holistic flow.
Implementing cellular production is a complex process but essentially calls for three broad steps:
Step 1 – Determine product families
The first step is to break down the final product into families, which are often parts or items with similar characteristics such as size, shape, and function. Items within the same family must follow the same – or very similar – production process.
Step 2 – Set up a cell for each family
Once the number of product families is determined, a work cell will be required for each one. All the equipment and materials needed to make the product family are included within the cell.
Cell workstations are typically arranged in a U shape, with dissimilar equipment placed close to each other to allow the operator to efficiently move from one step to the next. Operators must be proficient in all processes in their cell or assignment.
Step 3 – Optimize cell group organization
The floor layout and distance between cells are critical to overall productivity and efficiency. Conducting a production flow analysis can help determine the optimal layout to minimize distance, floor space, flow time, handling, scrap, etc.
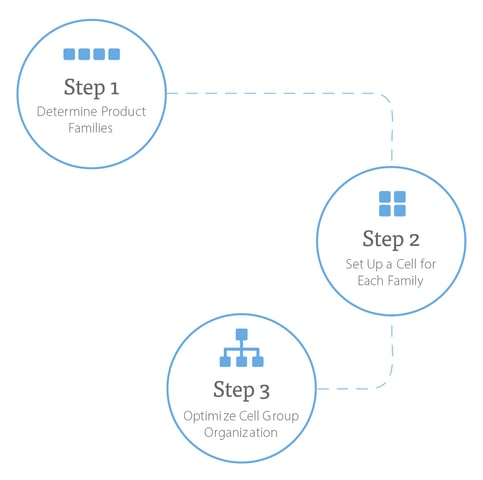
Other techniques to consider:
- Since space should be optimized within and between cells, using the smallest equipment for the job is typically recommended. Right-sized equipment saves room, allows for tight cells, and is easier to move around for production flexibility.
- When several products are to be produced with limited equipment, a single-minute exchange of die (SMED) system is recommended to minimize changeover time.
- Automation can be incorporated into cells to speed up throughput and allow operators to focus on hands-on aspects of production.
Tapecon’s approach
At Tapecon, our manufacturing cells are typically arranged by the printing process that best suits the application. Examples include:
- Screen printing: Membrane switches, graphic overlays, and printed electronics
- Digital printing: Durable labels, packaging
- Flexographic printing: Printed indicators, high-quality labels
Additionally, each cell includes the converting equipment needed to complete the product family, including cutting, laminating, packaging, etc. As part of our continuous improvement process, our team routinely evaluates the production flow and makes meaningful adjustments as needed.
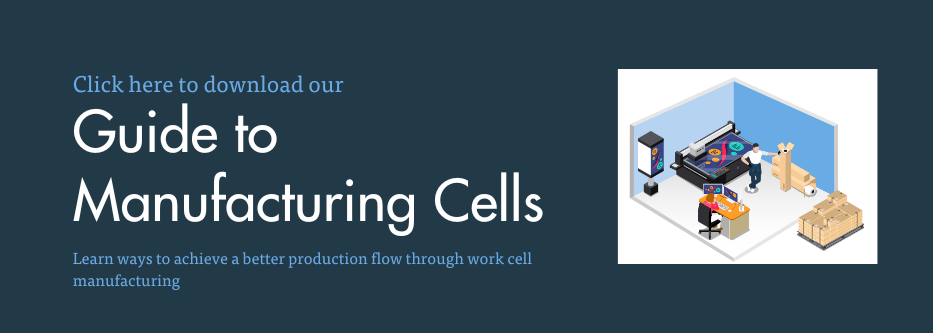
Let Tapecon make it.
With over 100 years of manufacturing experience, Tapecon works with product teams to solve challenges, create products, and enhance lives.
Contact Tapecon for a free, cross-functional discovery engagement to determine if outsourced manufacturing cells can deliver the strategic benefits and cost savings you need in today’s competitive market. We can also discuss a consultative feasibility study, including a portfolio review and recommendations for outsourcing implementation.