Growing up, we all learned the lesson, “It’s not what you say, it’s how you say it.” Similarly, when it comes to healthcare, sometimes it’s not just about what medication you take, but how you take it. One delivery method that has been around for over forty years but is growing in popularity is the transdermal patch.
In this article, we’ll scratch the surface of the benefits and design challenges for creating a high-quality and successful transdermal patch product.
What are transdermal patches?
Transdermal patches are designed for topical delivery of a medication or other substance. The patch is applied to the user’s skin, where a small, controlled, and consistent dose of the drug is absorbed into the skin and enters the bloodstream.
There are several advantages to using transdermal patches. They can be more convenient, non-invasive, and less painful than other drug delivery methods such as oral pills and intravenous injections. For caregivers and medical professionals, transdermal patches can improve medication adherence and decrease abuse. The patches can be especially beneficial for patients that require long-term and consistent therapeutic levels. In other words, the patient just needs to apply the product once – and the transdermal patch removes the possibility of missing a dose. Another benefit is that because the medication enters directly into the bloodstream, the drug isn’t broken down or affected by the body’s digestive processes.
However, there are a few limitations to keep in mind. While transdermal patches have been FDA-approved since 1979, not all types of medications can be administrated in this manner. Due to the defensive nature of the skin, the molecules of the active ingredient must be small enough to pass through and enter the bloodstream.
While the development process of transdermal patches can be long and complicated, working with an experienced manufacturing partner with the right materials expertise can improve speed to market and overall product quality.
Markets for transdermal patches
There are two broad markets for transdermal patches. The most established and highly regulated one being pharmaceuticals. Common medications used with transdermal patches include nicotine, scopolamine, rivastigmine, buprenorphine, and fentanyl.
An emerging market for transdermal patches is nutraceuticals. Used for recreational, supplemental, or general wellness purposes, these over-the-counter products are minimally regulated. Some popular nutraceutical applications of transdermal patches include cannabinoids (CBD, CBN), Vitamin B12, and Vitamin E.
Typical layers and constructions of a transdermal patch
While there are multiple constructions of a transdermal patch (which we’ll get to in a bit), most products consist of five layers or components.
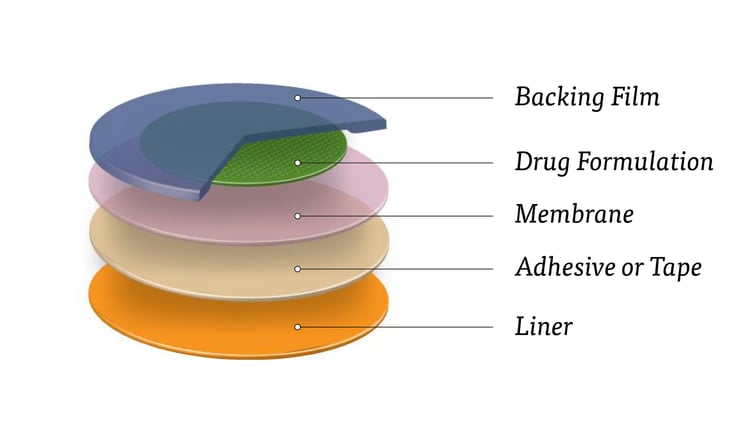
Images courtesy of 3M
- Backing film – The outermost layer that protects the drug formulation while the patient wears the patch. The backing can also be used as an area to print important product information or instructions. In some designs, the backing holds the drug formulation in place. For these reasons, material selection of backing film should consider durability and resiliency.
- Drug formulation – The active ingredient (or multiple ingredients) that will be diffused through the patch and absorbed into the user’s skin. This is sometimes referred to as the drug reservoir.
- Membrane – The design of the membrane determines the rate of drug formulation that is delivered into the skin.
- Liner – The layer protects the skin-contacting adhesive and is removed right before the patch is applied to the user. Though it seems like a very simple layer, the liner must be compatible with the adhesive and drug formula, be easy to remove (peel off), and meet regulatory requirements.
- Adhesive or tape – The bottom layer that uses skin-friendly adhesive to secure the patch to the user’s skin.
Depending on the drug being administered or the wear-time of the product, transdermal patches can be constructed in a few different ways.
- Drug-in-adhesive (DIA) – As the name implies, the active drug is mixed with a skin-friendly adhesive.
- Multi-laminate – When two drugs are required at different doses or release times, a membrane is inserted in the DIA layers.
- Reservoir – The drug formulation is encased within a pouch created by the backing and membrane.
- Polymer matrix – A polymer matrix reservoir is placed directly on the skin without the aid of a membrane layer.
Designing and manufacturing a transdermal patch
Before you can get your transdermal patch product into the hands (and on the skin) of consumers, there are many design challenges and manufacturing processes to tackle. As with any medication, it starts by getting the drug formulation just right. For transdermal patches, there’s the extra element of ensuring a controlled and consistent dosage. Another factor is the duration of use, which will influence both the drug formulation and the material selection of the patch (including stick-to-skin adhesives). Aside from the drug delivery mechanism, it’s important to consider comfort, ease of use (both applying and removing from the skin), and aesthetics of a transdermal patch.
Once the product has been thoroughly designed and tested, the manufacturing process of transdermal patches can be broken down into three main steps.
- Drug formulation mixing – This is where the dry powered drug is blended with the chosen adhesive (for DIA constructions), or the approved reservoir/matrix is created.
- Coating – The drug formulation (with or without membrane) is applied to the release liner. Additionally, the backing is laminated to the adhesive.
- Converting – Finally, the rolls are die-cut into the shape of the final patch. From there, the products are packaged and shipped.
At Tapecon, we have experience providing design consultation and custom converting for the medical device and pharmaceutical industries. Our facility is ISO 13485 certified and FDA Registered, with clean room converting capabilities. Plus, as a 3M Preferred Converter and converter of other reputable medical material suppliers, you can be confident you’re getting the highest level of converting expertise along with industry-leading materials for transdermal patches.
Let’s make something great
With over 100 years of manufacturing experience, Tapecon works with product teams to solve challenges, create products, and enhance lives. Learn more about our skin tapes and patches applications.