In this episode, we talked to Neil Bolding, Technical Manager at MacDermid Enthone Industrial Solutions about the evolution of membrane switches. Membrane switches first entered the manufacturing scene nearly 40 years ago, and iterations of the technology have never ended. Neil shares with us why this tech is so trustworthy and where he sees them heading in 2021 and beyond.
Watch the Video
Listen to the Audio
Conversation Overview
- Neil has been working with MacDermid Enthone since 1983, shortly after membrane switches were introduced to the manufacturing world.
- For a technology that has been around that long, why is it still projected to grow in the coming years? Neil attributes this to ASTM standardization.
- Through an ASTM committee, of which Neil is a participant, standards have been developed over two decades to test the durability and efficacy of different membrane switch materials and processes. Two to three times per year, experts in adhesives, films, printing, test houses, and design have aligned since 1991 to develop a common vernacular around this technology.
- What must be tested to prove the efficacy of a membrane switch? A switch must send and receive signals, so at least one layer must be moveable. Developers must ensure the flexing requirements are there, that the ink on the interior surface won’t degrade, or that the electrical circuit won’t decay over time. Abrasives and durability of solvents must also be tested.
- The testing standardization created by the collaboration of the ASTM is a primary reason why engineers feel confident in the performance of membrane switches. Through a lot of work and development and testing, companies can understand degradation and design around it.
- Through standardized testing procedures, membrane switch technology evolved from using polycarbonate films to polyester. Very early membrane switches used polycarbonate films, for which printing and cutting are easy and the result is relatively soft. Two drawbacks to polycarbonate films are a lack of a protective coat, making it easily broken or attacked by solvents, and minimal flexibility.
- Polyester is not as easy to print on as polycarbonate film, It needs to be processed with greater care and control. The same goes for cutting. Companies like Tapecon have experimented with printing and cutting processes. Now that that experimentation has been done, processes for printing on and cutting polyester have been established. Following these developments, we’ve seen inks created specifically for polyester films as well as adhesives to complement them.
- This testing and sharing of information is part of what allowed membrane switches to be refined to the point of the success we see with the technology today. There are around 34 different test method standards. 20 of those standards can be transitioned over to printed electronics which has helped progress in that technology, too.
- In this way, membrane switches are somewhat of a trailblazer, laying foundations for other technologies to thrive.
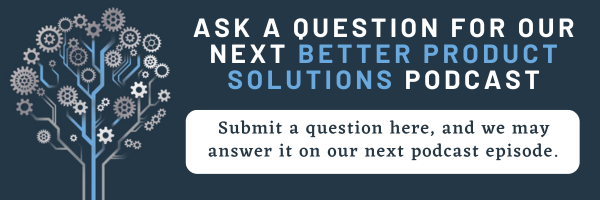
- Membrane switches aren’t going away, and they’re not standing still, either. New textures, digital printing integrations, and more advancements are being made today.
- Cleaning schedules have ramped up, thanks to COVID-19. How do membrane switches hold up to constant cleaning, and how is cleanability tested? Membrane switches have been traditionally durable to moisture, but testing has been done specifically around EPA-recognized virucides, as well as all sorts of chemicals. Tests focus on the environment in which a product will be used. Membrane switches used in medical devices are tested to all solvents that might be used in the arena of the medical field, for example. Testers soak films in cleaners or other solvents for 24 hours, they apply weights on different brushes to try to standardize what these cleaners and abrasions combined will do. THEN the film is tested for efficacy.
- Product engineers can find these ASTM standards to learn from them or to replicate tests on their own. A great place to start would be the ASTM website: https://www.astm.org/Standard/standards-and-publications.html
- Here’s where Neil sees the future of membrane switches heading, besides searching for price reduction methods:
- Dials and knobs will be replaced by more conventional types of switching.
- More switches will go touch-screen.
- He doesn’t see capacitive touch controls replacing membrane switches.
- The evolution of membrane switches is continuing. There may be lockdowns and a slowdown in business, but technology and research are not standing still.