How to Make Your Product Stand Out with In-Mold Decorating
Written by Casey Cephas
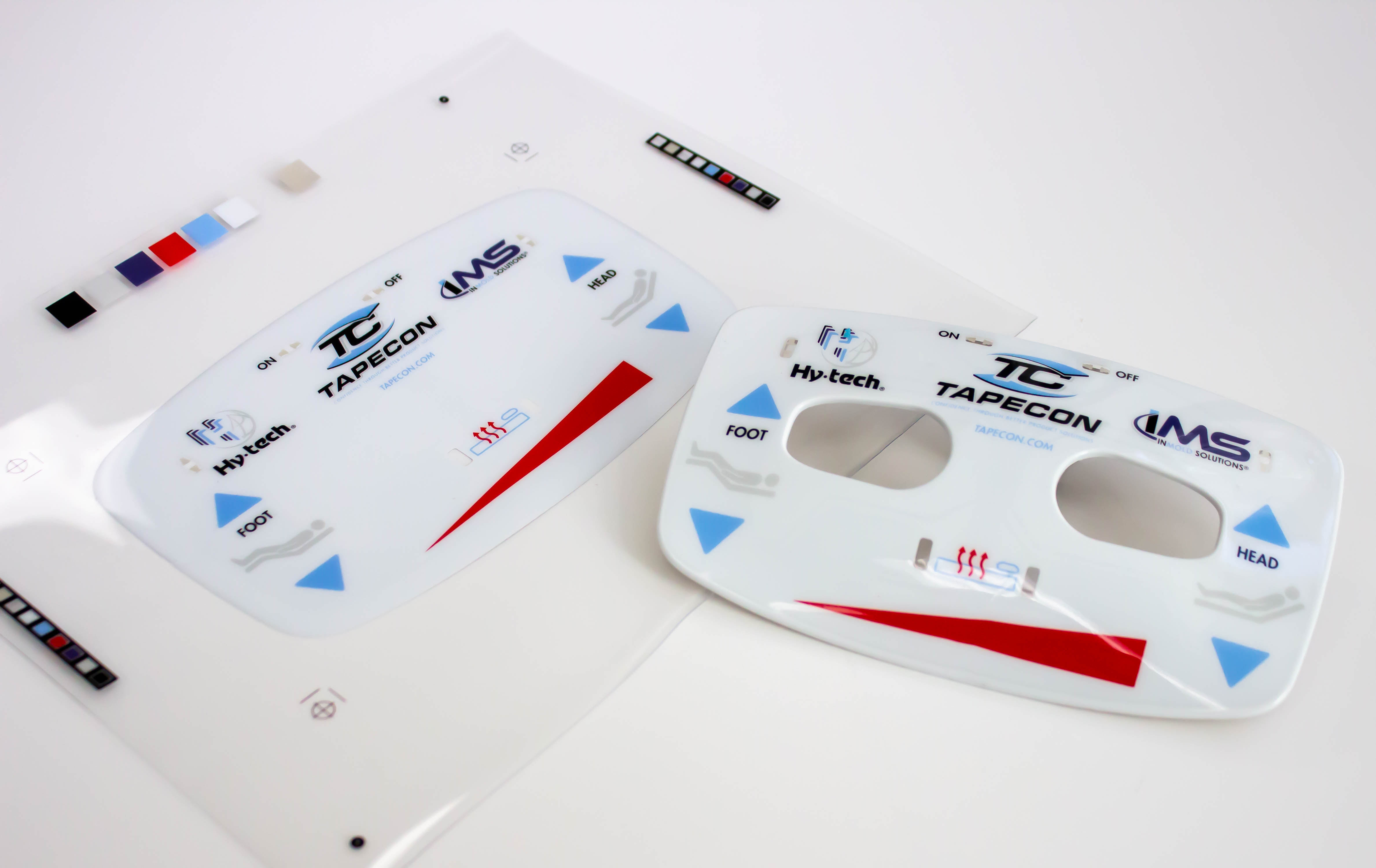
In today’s competitive market, it’s not enough for your product just to work – it also needs some “wow” factor. But thinking outside the box and coming up with a practical solution can be easier said than done.
However, there’s a process that you may not be using (or not utilizing to its full potential) that can improve the look, function, and durability of your product – all at once. No, it’s not magic. It’s in-mold decorating.
What is in-mold decorating?
In-mold decorating is used to create plastic components with graphics elements incorporated into the structure. In other words, the graphics are “baked” into the product, opposed to relying on secondary decorating methods such as adhesive labels and painting.
Here’s a quick rundown of how in-mold decorating works:
- A graphic overlay is printed on a special film to create an appliqué
- The film is cut and formed to the shape of the part being created
- The appliqué is placed into an injection mold
- Resin is added behind the appliqué
- When the resin cools, the graphics are permanently sealed into the plastic
The in-mold decorating process is versatile, requires less labor, and reduces waste. So how can it help your product stand out? We’re glad you asked.
Create high-quality, 3D graphics
In-mold decorating removes many of the limitations and frustrating aspects of post-mold decorating – especially when it comes to curved parts or 3D areas. Thanks to advancements in printing technology, designers have various printing options at their disposal, including colors, textures, and effects. The end result? Elegant, vibrant, and photo-realistic graphics integrated into your product.
Enable product differentiation.
In-mold decorating opens the door to creative design options that would be too difficult or expensive with other methods. Virtually any shape you can create with injection molding can feature branding, graphic elements, instructional text, and more.
Improve quality and durability
When creating a high-quality, durable product, the notion that “less is more” often holds true. Combining the plastic form and decoration eliminates a layer that can affect performance or wear out prematurely. You don’t have to worry about whether a label will fit or if the paint will wear off. What’s more, you can add coatings to the in-mold process to enhance the graphic overlay’s resistance to abrasion, chemicals, and other factors.
Incorporate unique or advanced features
With in-mold decorating, you’re not restricted to adding just printed graphic elements. Other surface features that can be added include windows, lenses, embossing, and more. You can also add in-mold electronics to create backlighting, indicators, dead fronting, and capacitive touch, just to name a few.
When to consider in-mold decorating
As you can tell, in-mold decorating can offer a host of advantages – but it’s not perfect for all applications. Here are a few considerations that will help you determine if in-mold decorating is suitable for your product.
- Type and shape of surface being decorated. In-mold decorating is most beneficial for complex or curved plastic parts – surfaces where other secondary decorating methods struggle. You can still use in-mold decorating on flat surfaces, especially if your product falls into any other categories below.
- Durability requirements. If your product has a long service life or is exposed to harsh environments, in-mold decorating can help add ruggedness to graphic elements and instructional text.
- Short-term versus long-term costs. In-mold decorating can come with a higher upfront price tag to set up the tooling. If you have a small or short run product, this can affect the per-unit cost. However, if you’re taking a long-term view, IMD can be a good investment.
- Changing graphics with the same tool. Once the injection mold tooling is created, it’s straightforward (and cost-effective) to change the graphics by printing and inserting a new appliqué.
- Eliminating adhesive from the product. Whether for functional, economic, or environmental reasons, you may be looking to remove adhesives from your design. In-mold decorating can help you accomplish this goal without sacrificing printed graphic quality.
Choose a manufacturing partner for in-mold decorating
Once you decide that in-mold decorating is the right solution for your product – or you need help weighing your options – it’s time to talk with an outsourced manufacturer with experience in this area. In-mold decorating can be a complex, specialized process that requires knowledge and precision to produce a high-quality part.
At Tapecon, we have over 20 years of experience using in-mold decorating to produce beautiful, durable products for our customers. Our team is ready to assist from start to finish, including design consulting, material selection, all the way to packaging and fulfillment.
Let’s make something great
With over 100 years of manufacturing experience, Tapecon works with product teams to solve challenges, create products, and enhance lives. Learn more about our in-mold decorating applications.